Conducting extensive and precise micromechanics analyses
The possibility to directly integrate microscopic, mechanical functional units with semiconductor electronics at silicon level gave rise to a multitude of different micromechanical sensors and actuators and to the huge success of MEMS and microstructures. The sheer range of product types and areas of use is huge.
The variety of device type encompasses pressure and inertial sensor systems for automotive and aerospace applications, MEMS microphones, MEMS acceleration and gyroscope sensors for portable electronic devices, a wide range of micro mirror elements for light manipulation, energy harvesters for autonomous systems and microbalances for extremely small material quantities. And, lastly, there are pMUTs and cMUTs for generating ultrasonics in medical technology and micro-acoustic elements such as SAWs, which are increasingly being put to use as electronic filter elements, but are also deployed in lab-on-a-chip applications too.
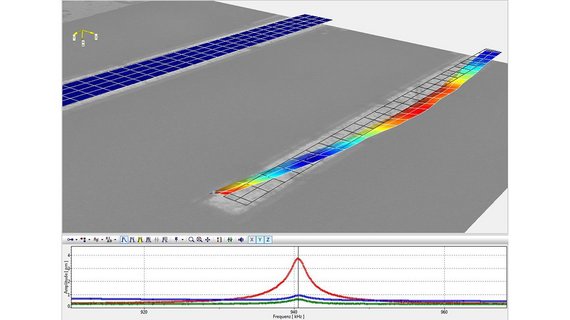
Capturing both in-plane and out-of plane motions
Reliable and precise measurement of not only the electrical measuring technology, but also the direct mechanical function – in other words, the movement of the smallest silicon components – is absolutely essential to developing MEMS components such as this. Using the microscope based single-point or scanning vibrometers from Polytec, you can measure displacements in the pm range, and acquire transfer functions and operational deflection shapes in either 1D or 3D, with a high frequency bandwidth and lateral resolution in the µm or sub-µm range. You also have the option of capturing your microsystem’s topography with the MSA Micro System Analyzer. The MSA-100-3D Micro System Analyzer allows for a real 3D vibration measurement with pm path resolution for both out-of-plane (OOP) and in-plane (IP) components. Here, this is taking place on an MEMS cantilever.