warranty on new sensors incl. laser diode
sensor exchange program
(excl. shipping)
buidlng laser sensors
customers being long-time partners
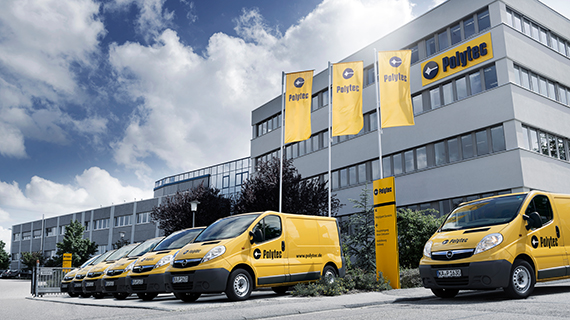
As a pioneer in optical measurement technology based in southern Germany, Polytec GmbH focuses on sustainable industrial partnerships - particularly in the field of optical speed and length sensors for industrial process control. The latest certifications according to ISO 9001 and ISO 14001 underline our environmental commitment. Our comprehensive services adress the core requirements of any manufacturing industry:
- Responsibility
- Precision
- Reliability
Join the transformation of production processes, stay future-proof and secure your leading position in challenging markets.
Your concerns matter - how can we help?
Our PolyXpert services measure customer satisfaction

3 year warranty incl. laser diode
Polytec stands behind the durability and performance of its optical sensors by offering an industry-leading 3-year warranty. This reflects our confidence in the quality and longevity of our products.
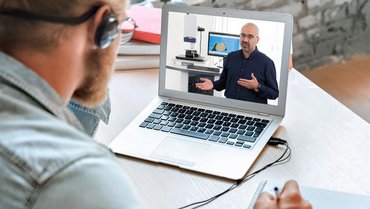
Swift reaction times
We stand by your side, proved by our typical reaction times below 4hrs per phone, 24hrs per e-mail and onsite support scheduled on request. We set your demands of modern production environments as our priority.
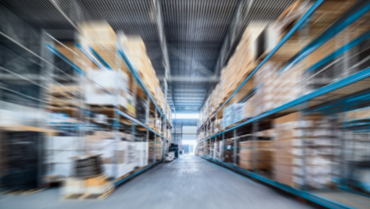
Always ready - sensor exchange program
Our sensor exchange program ensures continuous production by providing a seamless and efficient process for replacing sensors - usually within 24 hours (plus shipping, transition etc). When it comes down to issues, we help minimize disruptions and hold up your productivity.
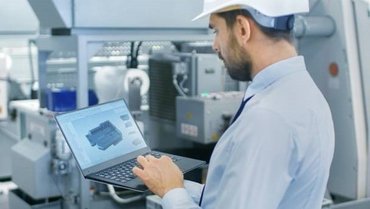
Commissioning & onsite support
Planning your next project and need assistance during early stages? We help you early on with our widespread application expertise and knowledge of industrial processes. Ask for a demonstration and onsite proof-of-concept. We are ready to assist you in custom integration, using a vast portfolio of application-specific accessories to really match the needs of your production line. We also help you with professional commissioning onsite and support you from mechanical through data integration.
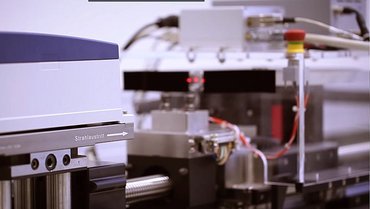
Schedule your calibration & maintenance
Uncompromised quality management, compliance according to ISO:9001 or others? Plan your next move and stay on the safe side. Scheduled calibration and repair is usually done in two working days. We offer calibration services, and ongoing maintenance support to guarantee the optimal performance of our optical sensors.
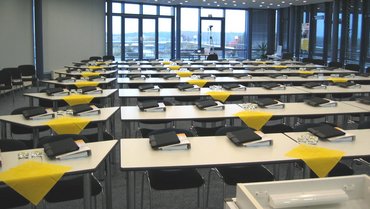
Trainings
Our global team shows an average of over 10 years of experience in the field, bringing unparalleled knowledge in a broad variety of industries. Upon request we also offer worldwide trainings to share our knowledge and experience and help you make the most of your investment.
Let's talk service packages!
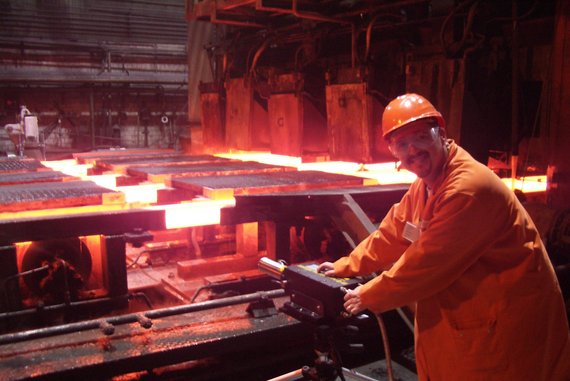
Proof of concept & live demonstration
Join us in transforming your production processes and securing your leading position in challenging markets. Live and onsite demonstrations and measurement data provide transparency, revealing what is possible. We measure process optimization - test it!