表面パラメータ
ワークピースの機械設計では、粗さやリップルなどの定義されたパラメータの仕様が含まれていることがよくあります。ポリテックの白色干渉計 非接触表面粗さ・形状測定機は、接触式の測定方法では長い時間を要する3Dプロファイル全体をわずか数秒で取得します。このようなパラメータ(例えば、接触面積の割合や周波数分布など)は、迅速かつ容易に決定することができます。粗さは非接触で測定することもできますが、その値は、図面の寸法や規格が参照する接触式測定の結果とは異なる場合があります。しかし、ポリテックの白色干渉計を校正するための新しいガイドラインにより、ユーザは測定値が校正基準にまで遡ることができることを保証されます。非接触測定では、粗さのパラメータも利用できます。例えば、ダイナミックシールの表面が粗すぎて摩擦損失が大きくなるのか、それとも滑らかすぎて接着力が過剰になってしまうのかを判断するだけで十分な場合もあります。
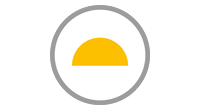
形状パラメータ
ワークピースを製造する際には、特に技術的、機能的、精密な表面の分野では、ごくわずかな細部、最も厳しい製造公差が表面の性能に影響を与えます。ここでは、メーカーは、すべての重要な寸法が要求された仕様を満たしていることを確認するために、形状、サイズ、テクスチャーなどの様々な形状公差や、平行度や角度などのその他の位置公差を正確に検査し、数値化する必要があります。ポリテックの非接触表面粗さ・形状測定機 TopMap シリーズは、精密部品の最も厳しい公差に対応するために特別に開発されました。
平坦性と平行性
機能表面の場合、燃料噴射システムやポンプのシール面などの精密部品の平面度や平行度など、特定のパラメータを測定することが重要になることがよくあります。このような表面は、高圧下で機能するように設計されており、製造工程の中で不可欠なステップとして、よく作られ、一貫して作られ、常に品質をチェックする必要があります。ポリテックの 3D 非接触表面粗さ・形状測定機 TopMapシリーズは、自動化と使いやすさを重視して設計されており、正確な測定データを生産工程への信頼性の高いフィードバックとして提供します。TopMap は、広い視野 (FoV) での平行度や平面度の正確な評価を、生産現場や品質管理ラボで直接行うことができ、重要な部品の評価を迅速かつ包括的に行うことができます。
高さと段差
段差、角度、表面間の相互作用の3D検査には、しばしば大きな垂直方向の測定範囲が必要となります。ポリテックの 白色干渉計 非接触表面粗さ・形状測定機 TopMap シリーズは、機種によっては最大 70 mm 以上の大きな垂直測定範囲を提供します。この大きな垂直方向の測定範囲により、小さな段差から大きな段差まで、深い凹みのある表面など、アクセスが困難な表面でも測定することができます。TopMapはテレセントリック光学設計を採用しており、影の影響を受けずに、重要なナノ、マイクロ、マクロの段差を確実に測定することができます。パターン認識などの自動化されたソフトウェアにより、データ処理が最適化され、複雑な機械的なワークの固定が不要になります。このような自動化の強化により、スピード、スループット、データ品質が大幅に向上しています。
表面粗さ
品質管理、研究、製品開発、生産において、表面粗さを正確かつ安定的に測定することは、品質を維持するためにしばしば決定的な意味を持ちます。従来のプロファイルパラメータは2Dであることが多い。これらの粗さパラメータは「R」パラメータと呼ばれ、確立され、よく理解されています。ここでは、機能的な表面の相互作用が面的な分析を必要とするため、3D面的な「S」パラメータが補助的に機能します。表面のトポグラフィーは3次元的な性質を持っています。単一のラインプロファイルでは、ピットや谷、ピークやリッジを識別することはできません。プロファイルやセクションの測定と分析は、たとえ適切に管理されていたとしても、実際の表面トポグラフィを不完全にしか説明できません。面的な表面形状は、はるかに包括的な情報を提供します。ポリテックの 3D 非接触表面粗さ・形状測定機 TopMap シリーズは、ISO 25178-2、ISO 4287、ISO 4288 に準拠した 2D および 3D の面状パラメータを提供します。
マイクロストラクチャ
マイクロストラクチャ(微細構造)とは、人間の目では見ることが難しい非常に小さな構造のことです。これらの表面タイプの機能は、マイクロメートルやナノメートルレベルの欠陥の小さな物理的変化によって影響を受ける可能性があります。そのため、高解像度の表面検査は、マイクロシステム技術の分野における表面特性評価の重要な側面となっています。ポリテックの非接触表面粗さ・形状測定機 TopMaps シリーズの顕微鏡ベースの表面形状測定機は、表面の詳細を迅速かつ非侵襲的に検査し、優れた再現性を実現します。3D 非接触表面粗さ・形状測定機 TopMap シリーズは、マイクロ・ナノデバイス、微細構造、複雑な表面、マイクロシステムの信頼性の高い安定した特性評価を行うための最良の選択です。
Table of surface parameter ISO standards
The mathematical description of numerous surface parameters can be found in various international standards. In practical application, ISO 4287 and ISO 13565 for 2D parameters and ISO 25178 for areal surface roughness are of particular importance. These standards define and describe the commonly used texture parameters. For the large number of parameters from profile standards, an equivalent areal parameter can be found in the published standard. Beyond that, areal topography evaluation offers additional benefit due to third dimension.
The amplitude or height surface parameters frequently used in practice were mostly extended to the areal evaluation. The areal evaluation of the topography shows the advantage of the measuring position being less sensitive than in profile-based evaluations, thus providing more reliable measurement results, especially for inhomogeneous and defective surfaces. However, the surface parameter family as a whole has in common that they cannot represent the functional differences between different types of surfaces. This means that differently manufactured and designed surfaces might still show the same results with respect to the surface parameters.