How continuous casting benefits from optical sensors
Here is why ProSpeed® LSV laser sensors allowing a non-contact inline measurement of casting speed and length are the metrology of choice for steel process control, especially in challenging industrial environments like on red-hot steel and continuous casting machine processes – wether for slabs, billets, blooms or at the torch cutter.
The ProSpeed® optical speed and length sensors using the laser Doppler velocimetry principle are designed for high-precision, reliable, non-contact length & speed measurement for continuous casting. Avoiding contact and influence with the surface and being wear-free sparing any moving parts, it avoids drawbacks of traditional measurement methods, such as slippage, wear & tear or changing wheel diameter. Its mill duty construction, excellent repeatability and long term reliability make it an integral component for improving cut length tolerance, minimizing maintenance and increasing production efficiency. The result is reduced scrap and optimized yield at the caster, rolling mill and overall plant operations.
Relevance of optical sensors for the continous casting process
There is a direct correlation between length and speed over the time constant. So, measuring speed in a continuous process also results in gathering the length of the measured product. Typically, all inline measurement methods use this correlation.
But why and where in continuous casting is the knowledge about the exact length and speed of the product relevant for a steel, aluminum or metal manufacturing process?
- For precise control of the cut length on continuous casters
- For avoiding slippage of tactile measurements
- For wear-free and downtime-optimized operation
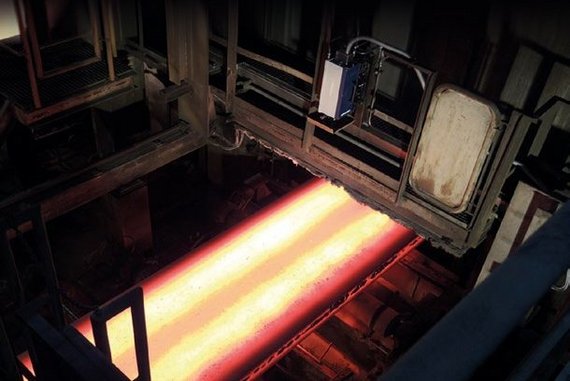
Sensors designed for harsh casting environments
The rugged, mill duty construction, sophisticated optical configuration and advanced signal conditioning, offer unmatched reliability and performance. A typical solution consists of a sensor head with 1500 mm stand-off distance, water-cooled housing, air wipe and various outputs for easy integration to existing control systems. The efficient water-cooled housing saves additional equipment.
Continuous casting emission calculation and savings potential
Taking a 5-strand billet caster with 220 square millimeter billets cut to 6-meter length each and considering the density of steel as 7,85 kg/dm³, the cast billets produced weigh 379,94 kg/m. A typical caster would operate at 900 mm/min cast speed at a 24h/day operation. Bringing together the numbers results in 1,080 cuts a day, considering all 5 strands. Using measurement wheels or similar technology in a rough environment will lead to an average accuracy of 1% whereas using an LSV realistically will provide an accuracy of 0,1%. So, the average improvement per cut is roughly 24mm. The resulting figures of this improvement are shown in table 1.
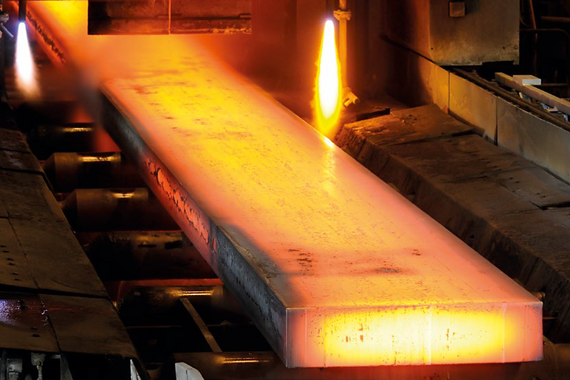
Cut-to-length in continuous casting
The task of cut-to-length is an absolute must in every continuous caster. Measuring the cast length and triggering the cutting process needs to be implemented in every casting mill. Generally, no matter the shape, subsequent processes or final end product, the strand needs to be cut after casting. Otherwise, the following handling of the product is impossible. As the general casting speed varies, measuring the length of the product to determine when to cut is inevitable.
The product length is important for following processes especially when a certain final length of the product is needed e.g., in rail production. Generally, the better the consistency of incoming length, the more accurate the following processes can be regulated and the higher the quality of the end product. Reliable precision in the length of a product are key especially for SPQ-steel (superior product quality) in product trading business.
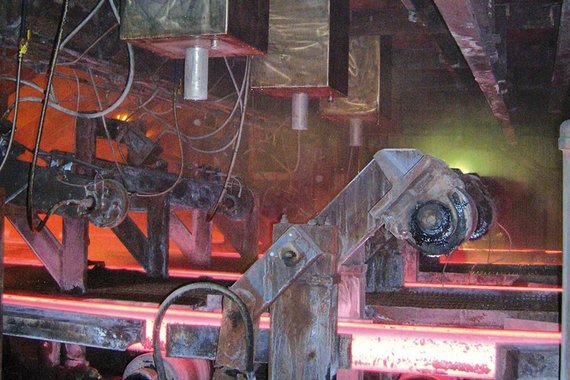
Process control in continuous casting
For certain process steps during continuous casting knowing the speed of the product is an essential control parameter. One important part of the process is the cool-down section where the transition between liquid and solid phase of the material takes place. The speed determines major characteristics of metallurgy and material properties and therefore knowledge of the casting speed is very important. Another example is speed synchronization of a flying torch or saw in order to precisely claw the cutter to the material and perform a clean cut with minimal tolerances and minimum impact on the equipment.
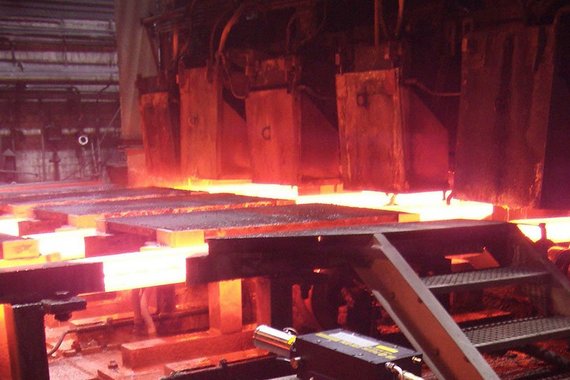
Weight determination in steel casting
Another major usage of length information is to determine the weight of the product much earlier in the process than possible with a weighing system. In a clean casting process the outer shape of the product is determined by the coquille early in the process and does not change during the following process. The specific weight of the product is a result of its ingredients and determined even earlier in the mold. Knowing the length of the product even before the cut can lead to very low tolerances in final weight as process fluctuations can be addressed early in the process leading to optimal process consistency. If planned upfront the mill can also save the integrated scale and use a speed measurement method instead.
Relevance of casting and global role of steel production
According to the World Steel Association roughly 7 % to 9 % of the entire global CO2 emissions are directly related to the production of steel and non-ferrous metals.1 This results in around one third of the total emissions generated worldwide, in all industries combined.2 The World Steel Association, which represents more than 80 % of global steel production including casting, rolling and more, agreed on a program called “Step Up” in order to address specific actions aiming in the direction of improving the steel industries sustainability impacts.3
1 World Steel Association 2021, Climate change and the production of iron and steel, accessed 1 February 2023, https://worldsteel.org/publications/policy-papers/climate-change-policy-paper
2 Hannah Ritchie and Max Roser, n.d., Emissions by sector, accessed 1 February 2023, https://ourworldindata.org/emissions-by-sector
3 World Steel Association, n.d., Step up programme, accessed 1 February 2023, https://worldsteel.org/steel-topics/technology/step-up-programme
Images courtesy: Images courtesy of Polytec GmbH unless otherwise specified.