Measuring form deviation and roughness together
The surface quality of raw products is crucial to guaranteeing that products will work perfectly later on. Metallic implants in dentistry, for instance, require a particularly low level of roughness. In contrast, many raw products depend on a particular level of roughness for subsequent painting and coating processes. Some applications even call for concurrent information about form deviation and roughness. The TopMap models from Polytec allow both the large area determination of form deviation with nanometer resolution and a large measurement volume plus the measure of surface roughness on a smaller section. While whitelight interferometry allows areal surface inspection, the additional chromatic confocal sensor determines roughness profiles, too. Characterize entire workpiece surfaces, calculate volume and exactly determine peaks and valleys on behalf of the examined distance parameters.
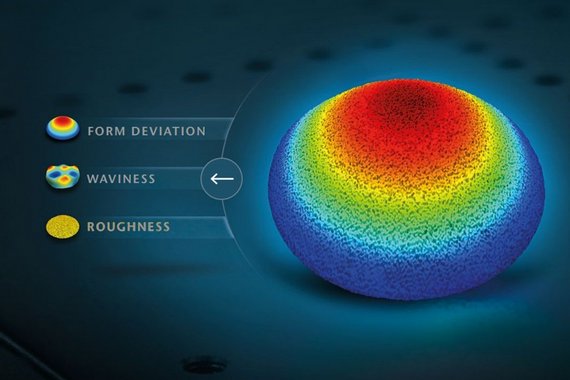
Classification of form deviation and other surface components
What's the difference between surface form, surface roughness and surface waviness? By conventional machining processes, three main components of surface topography are generated and they are classified according to their causes. The first component are the roughness and texturural details which are inherent in any production process, left by machining (e.g. cutting tool, spark), as a result of edge formation or tool tip irregularities. Second component is the waviness which results from factors such as deflections, vibrations, unbalanced grinding wheel, irregularities in tool feed, chatter or extraneous influences. The third surface component after roughness and waviness is the form or shape, characterizing the exact geometric properties with regard to the form tolerance values defined in technical drawings and designing.
Download whitepaper
Form deviation, waviness or flatness, and roughness or texture are not sharply defined but rather defined close to each other. A surface can be described as a superposition of numerous wavelengths, where the transition within surface components from form (particularly long-wavelength) over waviness to short wavelength roughness components takes place smoothly. Read more in the surface roughness whitepaper.