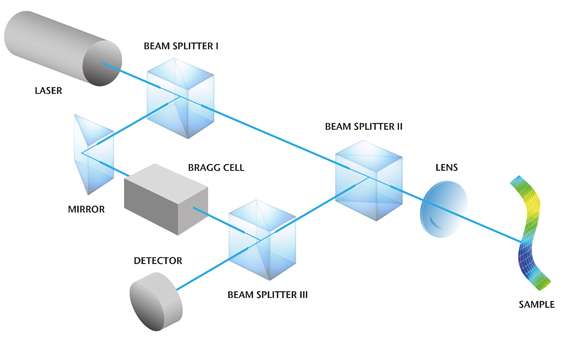
Laser Doppler vibrometry
Laser Doppler vibrometry (LDV) is currently the method that offers the best displacement and velocity resolution and is used in many fields of basic science. It enables femtometer amplitude resolution and is linear and therefore has a consistent amplitude right up to the very high frequency ranges – practically reaching more than 6 GHz at present. These properties are independent of the measuring distance, so this principle is used both in microscopic operations and over very large distances. Light as a sensor does not influence the sample, making it non-invasive and therefore enabling measurements to be carried out on extremely small and extremely lightweight structures. Since this procedure offers such unbeatable properties, Polytec has made it robust and fit for use in both the laboratory and outdoors.
Basic principles of laser Doppler vibrometry
Laser vibrometry focusing on the small details
Characterize small and delicate structures in a non-contact way. Analyze vibration, acoustics and dynamics. Measure biomedical samples, electronics components and microstructures like MEMS by light, without mass-loading, and from DC up to the GHz range on a large bandwidth. Laser vibrometers focus on the small details, measuring deflection shapes for model validation. They assess the frequency response and determine resonance frequency, impulse response and Q factor. No matter how big or small – Polytec vibrometers measure it!
Laser Doppler vibrometry featuring QTec® multipath interferometry
QTec® reinvents laser Doppler vibrometry by eliminating the root cause of noise, leading to superior optical sensitivity and high-fidelity measurements on all surfaces. QTec laser Doppler vibrometers from Polytec use an innovative multi-path interferometer concept utilizing the highest quality signal of each path to achieve the best results. This patented technology is combined with the well-proven infrared Xtra sensor design for faster, easier measurements and a consistent result.
More about Laser Doppler vibrometry in a free demo or feasibility study?
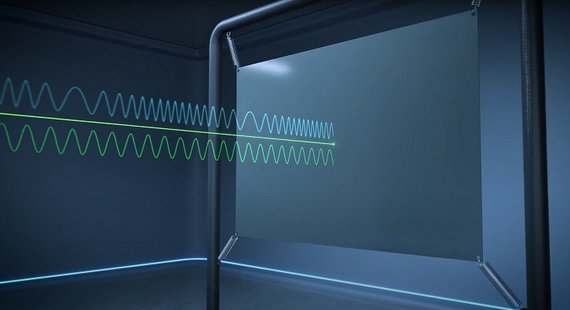
The Doppler effect
If a wave is reflected by a moving object and detected by an instrument (as is the case with the LDV), the measured frequency shift of the wave can be described as:
fD = 2· v/λ
where v is the object’s velocity and λ is the wavelength of the emitted wave. To be able to conversely determine the velocity of an object, the (Doppler) frequency shift has to be measured at a known wavelength. This is done in the LDV by using a laser interferometer.
Interferometry
Laser Doppler vibrometry works on the basis of optical interference, whereby essentially two coherent light beams, with their respective light intensities I1 and I2, are required to overlap. The total intensity of both beams is not just the sum of the single intensities, but is modulated according to the formula:
Itot = I1 + I2 + 2 √(I1 I2) cos [2π(r1 - r2)/λ]
with a so-called “interference” term. This interference term relates to the path length difference between both beams. If this difference is an integer multiple of the light wavelength, the total intensity is four times a single intensity.
The Doppler frequency shift
Changing the optical path length per unit of time manifests itself as the measurement beam’s Doppler frequency shift. In metrological terms, this means that the modulation frequency of the interference signal determined is directly proportional to the velocity of the sample. As object movement away from the interferometer generates the same modulation pattern (and modulation frequencies) as object movement towards the interferometer, this set-up alone cannot unambiguously determine the direction the object is moving in. For this purpose, an acousto-optic modulator (Bragg cell) that typically shifts the light frequency by 40 MHz is placed in the reference beam (for comparison purposes, the laser light’s frequency is 4.74 · 1014 Hz). This generates a typical interference signal modulation frequency of 40 MHz when the sample is at a standstill. If the object then moves towards the interferometer, this modulation frequency is increased, and if it moves away from the interferometer, the detector receives a frequency less than 40 MHz. This means that it is now possible to not only clearly detect the path length, but also the direction of movement too.
Displacement or velocity of vibrations
In principle, it is possible to directly measure displacements as well as velocities with the LDV. In this case, the Doppler frequency is not transformed into a voltage proportional to velocity; instead, the LDV counts the light / dark fringes on the detector. Using suitable interpolation techniques, Polytec’s vibrometers can thus attain a resolution of 2 nm, and with digital demodulation techniques this can even be extended as far down as the pm range. Displacement demodulation is better suited to low frequency measurements (in the sub Hz range), while velocity demodulation is better for higher frequencies, since the maximum amplitudes of harmonic vibrations can be expressed as follows:
v = 2π • f • s
As its frequency increases, a vibration generates a relatively high velocity at a very low displacement amplitude.