warranty on new profilers
experience per PolyXpert
satisfied customers worldwide
awards in optical technology
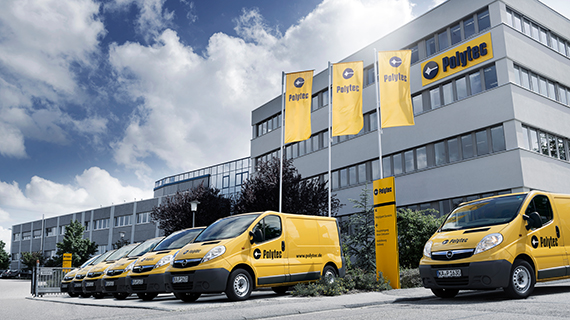
Polytec optical surface metrology allows characterizing precision surfaces areally, analyzing microstructures with sub-nm Z resolution - on rough surfaces like CNC machined or additive manufactured parts, as well as on smooth surfaces like wafer and optics. We care about the details. As a pioneer in optical measurement technology based in southern Germany, Polytec GmbH focuses on sustainable partnerships. The latest certifications according to ISO 9001 and ISO 14001 underline our environmental commitment. Our comprehensive services adress the core requirements of any manufacturing industry:
- Responsibility
- Precision
- Reliability
Join the transformation of production processes and quality control, stay future-proof and secure your leading position in challenging markets.
Your concerns matter - how can we help?
Our PolyXpert services measure customer satisfaction
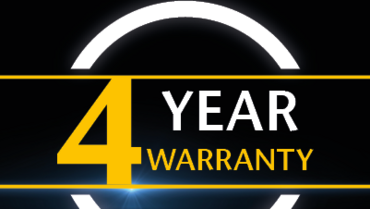
4 year warranty
Polytec stands behind the durability and performance of its surface metrology systems by offering a unique 4-year warranty, reflecting our confidence in the quality and longevity of our optical profilers.
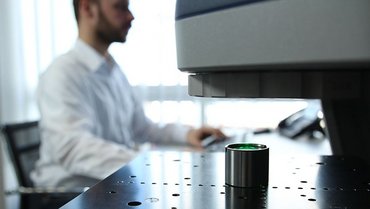
Measurement service & rentals
Our PolyXperts are looking forward to supporting you with flexible and custom measurement services in our modern labs or at your site - also remotely as online session! We’d be happy to guide and consult you at any stage. Besides outsourcing, ask for our rentals for expanding your capabilities on shorter notice.
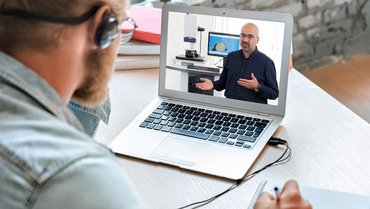
Trainings
Our global team shows an average of over 15 years of experience in the field, bringing unparalleled knowledge of surface inspection on precision mechanics, semiconductors, optical components and more. Upon request we offer custom trainings to help you make the most of your investment. Tell us about your topic and need!
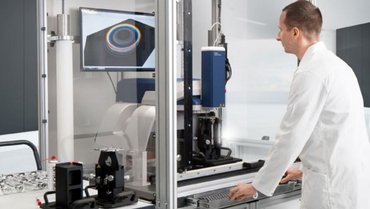
Customization
Sometimes our 44x33 mm large field of view (stitching 230x220 mm) is not enough or you need specific sample holders or vibration isolation. Sometimes our CST Continuous Scanning Technology with up to 100 mm vertical measurement range is just a piece of your puzzle. Are looking for automation or custom adaptions using SDK (Software Development Kit)? Together with you, we elaborate custom software + hardware + optics as one-stop solution, whether custom parameters or implementing measurement routines. Our surface topography solutions upon your specification.
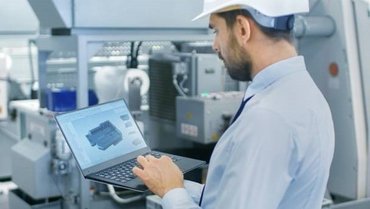
Commissioning & onsite support
Planning your next project and need assistance during early stages? We are ready to assist you in custom integration, using a vast portfolio of application-specific accessories to really match the needs of your quality control task. We also help you with professional commissioning onsite and support you from mechanical through data integration.
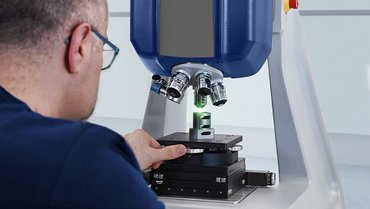
Schedule your calibration & maintenance
Uncompromised quality management, compliance according to ISO:9001 or others? Plan your next move and stay on the safe side. Scheduled calibration and repair is usually done in two working days. We offer calibration services, and ongoing maintenance support to guarantee the optimal performance of our optical sensors.
Custom measurement service & support
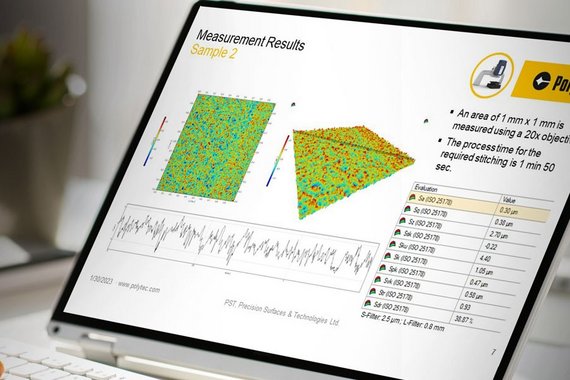
Free feasibilty & demo
Join us in transforming your production processes and quality control, securing your leading position in challenging markets. Our demonstrations and gathered measurement data on your real samples provide insights of what is possible. We measure your sample surfaces - send your sample! Because we believe in a mutual, long-term partnership, the initial feasibility study is for free.