Characterizing roping and determining the roping grade
Roping on aluminum (AL) alloy is a phenomena of surface structuring on automotive alloy sheets and car body panels. A related quality criteria is the formation of orange peel, which is basically the undesired waviness of surfaces. The appearance of roping or ridging is a visual defect that can be quantified measuring over large areas using 3D surface profilers from Polytec for non-contact, reliable and reproducible roping grade characterization.
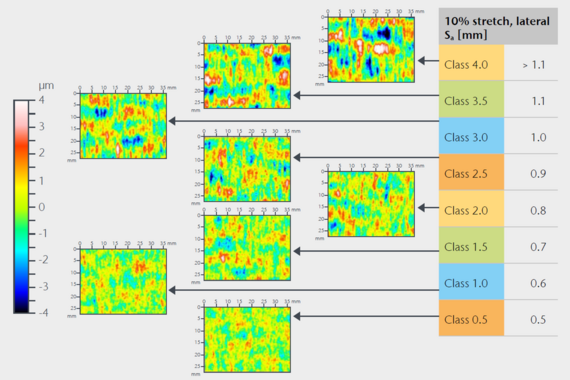
Roping as surface appearance of AL sheets for car body panels
Besides other advantages, aluminum alloys permit lightweight structural designs and innovative solutions to weight reduction in automotive applications. Consequently, the demand for aluminum alloys is growing rapidly for applications where strength-to-weight ratios are critical. Aluminum producers supply the market with unfinished aluminum alloys that must be rolled, stretched, and pressed into the appropriate shape. As a result of forming operations, the grain structure of the alloys is re-ordered, leading to an increase in surface roughness and an “orange peel” appearance.
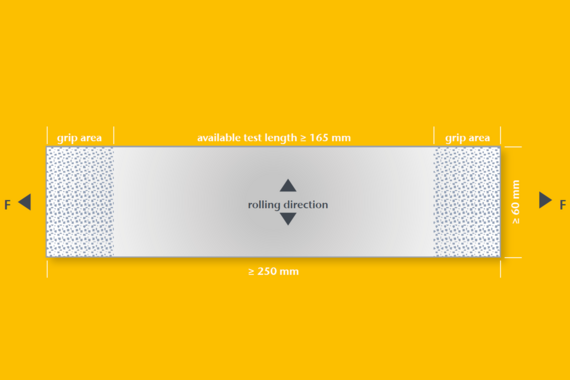
Cause of roping structures
Under certain conditions, the surface roughness can consolidate into larger banded or “roping” structures that appear parallel to the rolling direction and perpendicular to the stretching direction. Typically, the structure widths are between 0.2 to 2 mm, and the lengths are between 10 to 30 mm. The roping structures can be identified visually and destroy the appearance of the surface.
Sign up for the full roping paper
Contact us for roping characterization
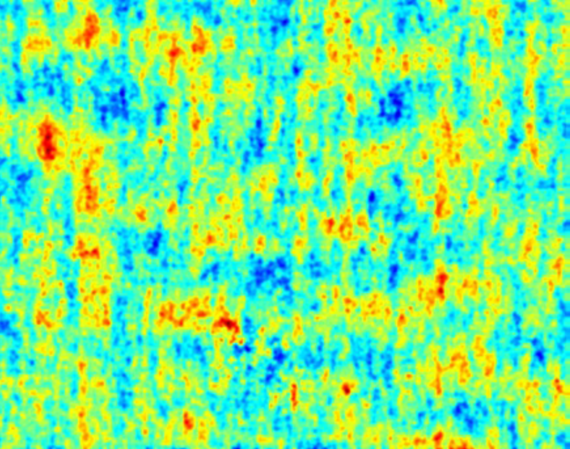
Roping grade determination using imprints
As a second approach to determine the roping grade, the German Association of the Automotive Industry (GAAI) recommendation VDA 239-400, which uses an imprint of the surface, can be applied. The imprint method has many similarities to making a copy of a credit card with raised font structures by placing a paper over the structures and rubbing with a pencil to make the raised font surfaces visible: the deep areas remain bright, and the high ones are darkened. Using specially prepared adhesive tape, an imprint is taken and scanned at 300 dpi to form a gray image. At this resolution, the small structures (roughness) that are not relevant are filtered out and are no longer recognizable. The grayscale values are indicators of the heights when the imprint process is done correctly. The gray image is evaluated by software, which calculates the roping degree based on the standard from 0 (no roping) to 9 (very strong roping). While this approach seems simple, it is labor-intensive, time-consuming, lacks precision and error-prone. These disadvantages are eliminated when using TopMap whitelight interferometers from Polytec.
To ensure that the measurement results are comparable to the GAAI standard, TopMap surface profilers feature an algorithm to prepare and export data for further processing for roping grade determination. In addition, the integrated surface metrology software calculates the RK parameter according to the VDA 239-400 GAAI.